Sintered metal chromium body (protection tube)
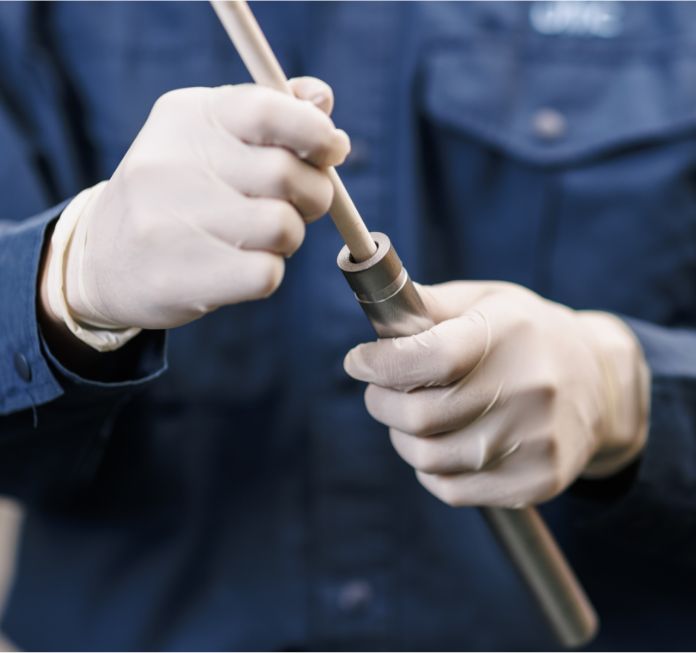
Metallic chromium has high thermal conductivity, a low coefficient of thermal expansion, and high oxidation resistance against various high-temperature gases (especially oxidizing gases). It is also resistant to corrosion from sulfur dioxide and methane. Furthermore, it demonstrates high resistance to corrosion even in high-temperature alkali environments. In addition, in boilers that use heavy oil as fuel, slag containing V2O5 is generated in the system. However, even under such conditions, it demonstrates exceptional resistance to corrosion compared to other metal materials and is resistant to extreme environments where ceramic materials would not be able to withstand such conditions.
Despite its exceptional properties, it is difficult to attain formability for metallic chromium, and there have been few examples of its practical use as a structural material.
We have successfully manufactured sintered metal chromium bodies without processing by fully utilizing our high-purity metallic chromium manufacturing technology and slip casting method, cultivated as a molding technology for ceramics.
Currently, it is used as a protection tube for thermocouples in waste incinerators or as boiler components.
Information on sintered metal chromium bodies
In 1998, we began developing metallic chromium products using the slip casting method and commercialized components (nozzles, thermocouple protection tubes, etc.) used in boilers, waste incinerators, etc., under extreme conditions.
-
Metal chromium protection tube
In recent years, high-temperature combustion systems have been adopted for waste incinerators to control dioxin, which is a carcinogenic substance. Thus, controlling the temperature inside the furnace is very important. However, under such high-temperature combustion (high-temperature corrosive environment), conventional high heat and corrosion resistant metals such as ceramics and Ni/Cr (50/50) have resulted in a short life span. The cause was erosion (corrosion and wear), and a material that could withstand these conditions was needed.
By using the slip casting method, we have developed a “thermocouple protection tube made of pure chromium with no welded joints,” which currently attracts inquiries from many plant manufacturers. The plant in which we have introduced the system on a trial basis has received the highest evaluation in Japan, and both the initial and operating costs are satisfactory.
-
Burner diffuser
In boilers using heavy oil, V, S, Na, and other elements contained in the fuel become V2O5-Na2SO4-type oil ash, which adheres to and accumulates on the surface of the components, causing significant oxidation of the components and early deterioration due to “vanadium attack.”
Burner diffusers made of metallic chromium are developed to solve the problem of short lifespans caused by vanadium attack.
Comparing boilers using heavy oil after six months of installation
Metallic chromium
NiCr 50/50
The pictures on the right represent the situation six months after installing the burner diffuser in a boiler using heavy oil. It can be seen that the corrosion resistance of the burner diffuser is much higher than that of the conventional NiCr50/50 diffuser.
Metal chromium has excellent properties such as high thermal conductivity, a low coefficient of thermal expansion, and high oxidation resistance against various high temperature gases (especially oxidizing gases). However, it is difficult to attain formability for metallic chromium, and there have been few examples of its practical use as a structural material. We have successfully manufactured sintered metal chromium bodies without processing by fully utilizing our high-purity metallic chromium manufacturing technology and slip casting method, cultivated as a molding technology for ceramics.
Characteristic table
-
- Purity
- More than 99.5%
-
- Bulk density
- 6.7g/cm3 or more
-
- Bending strength
- 400 MPa